The Challenge
A specialised sheet metal processing factory faced significant operational inefficiencies in their order management and production processes. The factory produces a diverse range of construction and decoration elements including window sills, metal lids, roofing panels, stovepipes, ventilation components, parapet elements, drip edges, gable flashing, and custom sheet metal profiles.
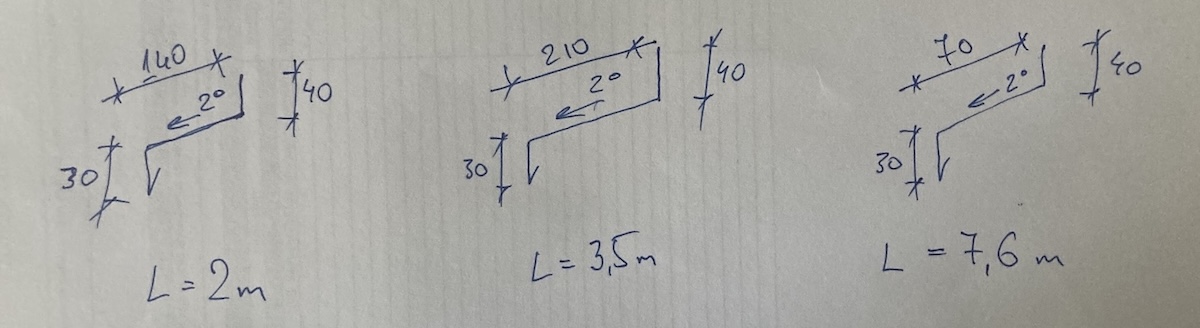
Three hand-drawn sketches of a window sill
One of the most pressing daily complexities was efficiently handling new client orders, particularly given that most ordered elements were unique in terms of size, color, and coating specifications. The factory's management relied heavily on traditional paper-based processes, collaborating with clients through hand-drawn sketches to communicate manufacturing details and specifications.
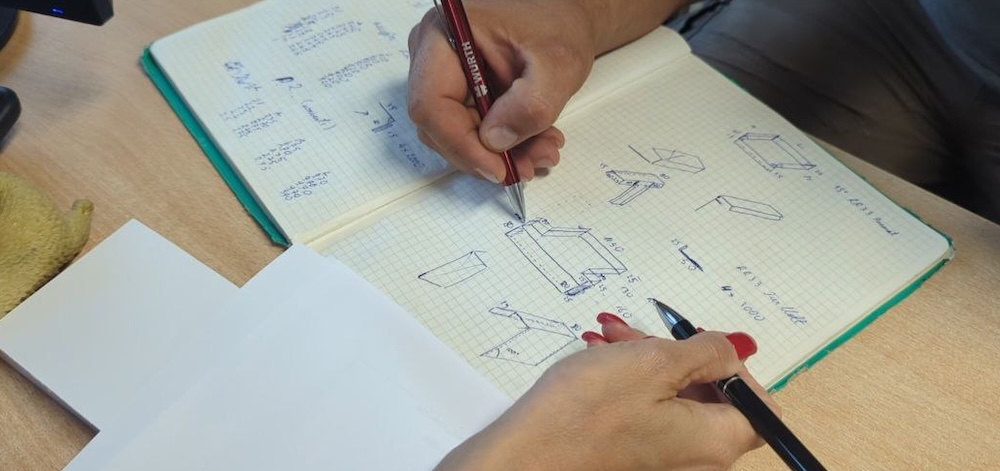
Collaborating with clients through hand-drawn sketches
This manual approach presented multiple critical challenges. Hand-written sketches were inherently prone to errors and lacked standardisation, creating potential for miscommunication and manufacturing mistakes.
The subsequent digitisation of these sketches became a time-consuming bottleneck that required additional CAD engineering hours, significantly impacting operational efficiency and increasing project turnaround times. The lack of real-time visualisation capabilities also made it difficult for clients to fully understand their orders before manufacturing commenced.
Our Approach
Our approach centered on creating an integrated system that would eliminate manual sketch-based workflows while providing enhanced visualisation and calculation capabilities.
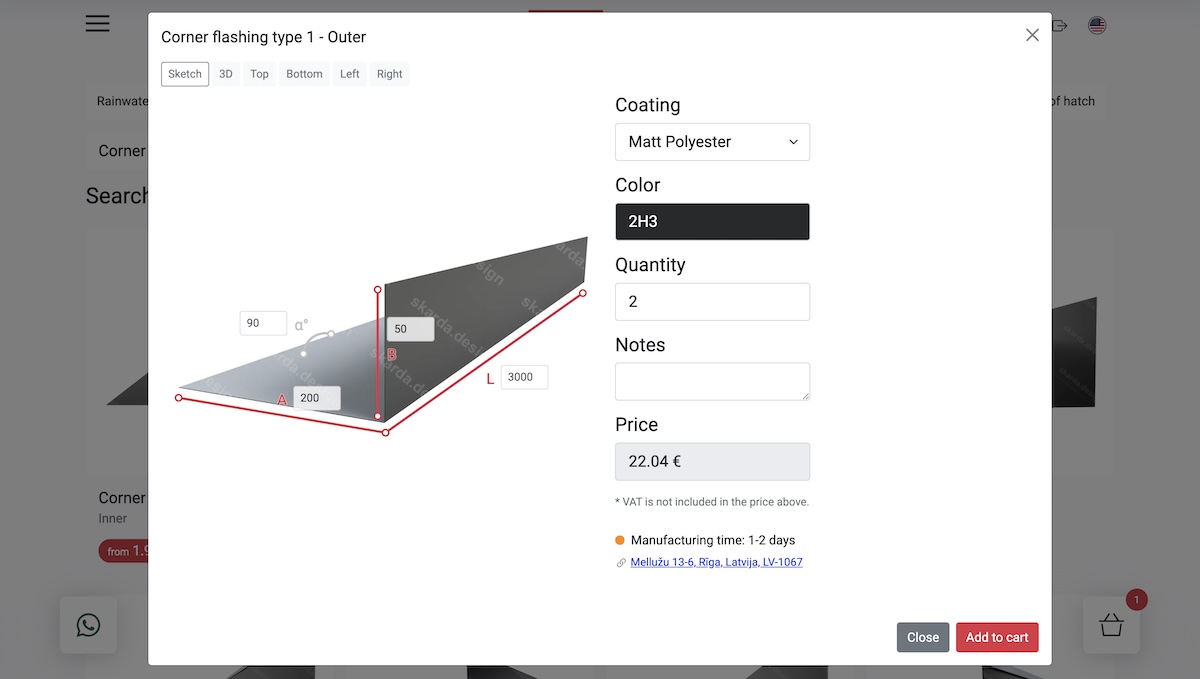
Customers can input custom size specifications
Our development strategy focused on creating a cloud-based platform that would be accessible across multiple devices and integrate smoothly with existing factory infrastructure, particularly Laser cutting machinery and customer relationship management systems (CRM).
Implementation Strategy
The Kenzap Factory solution was implemented through several interconnected modules, each addressing specific operational requirements:
- Element Classification and Grouping Module: This foundational component efficiently categorises and groups manufacturing elements, creating a structured approach to product management and enabling more efficient product search functionality.
- Element-Specific Formula Declaration: Factory management can declare and customise specific formulas for individual elements, which serve as the foundation for automated price calculations and material consumption estimates.
- Formula Integration with Sketch Elements: This module provides seamless linking between calculated data and corresponding visual sketch elements, ensuring consistency between pricing and design specifications.
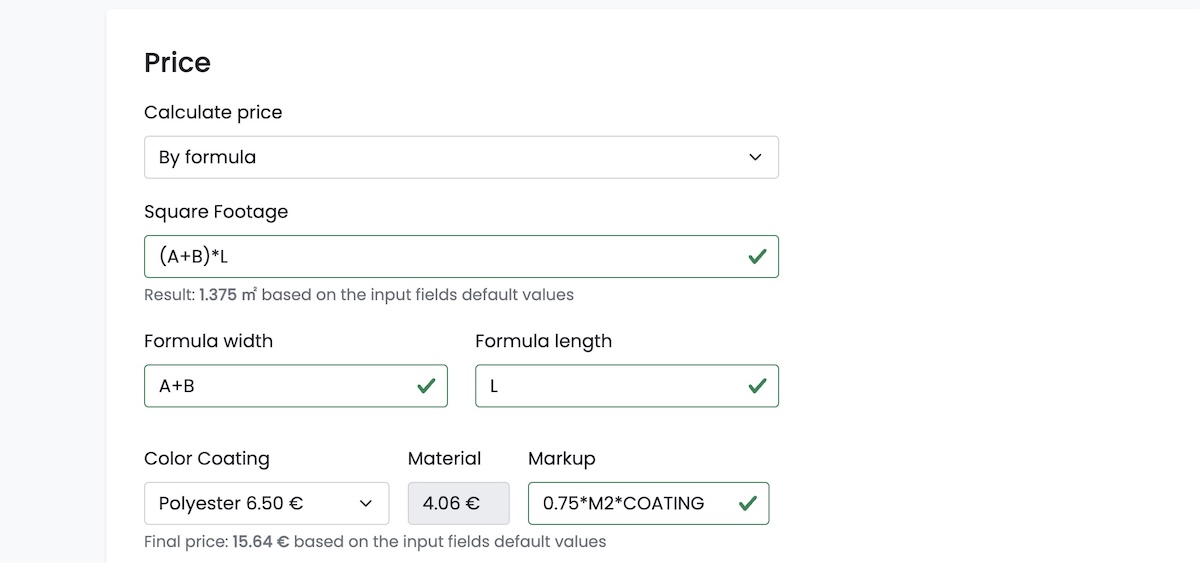
Element-Specific Formula Declaration
In addition, the platform supports webhook functionality to automatically transmit data when specific system events occur, ensuring real-time communication between different business systems.
A critical implementation component involved direct integration with factory CNC machines, enabling the automated transmission of programmatically modified 2D sketches upon order approval, creating a seamless transition from digital design to physical manufacturing.
Results and Impact
The implementation of Skarda Design platform generated significant measurable improvements across multiple operational areas. The solution successfully serves both end-consumers and factory management, creating value throughout the entire order-to-delivery process.
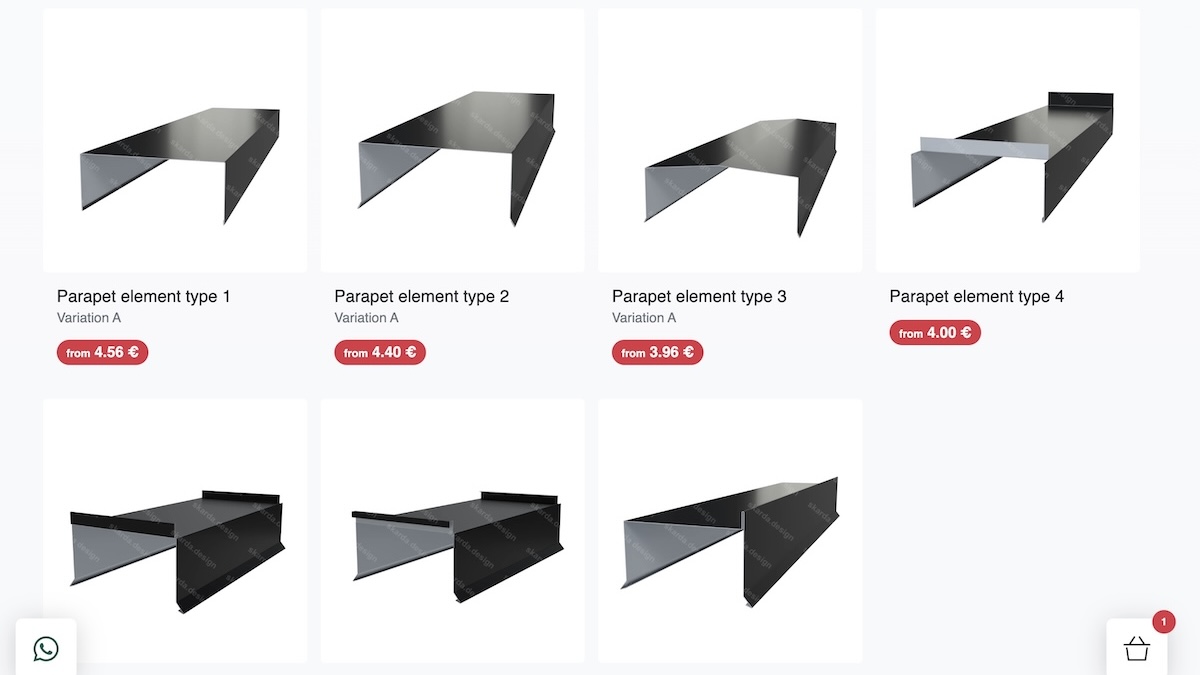
Element Classification and Grouping
For customer-facing operations, the platform enables convenient grouped and categorized element searches, coupled with 3D visualisation capabilities before actual manufacturing begins.
Customers can input custom size specifications directly through mobile or desktop browsers, generating live previews. The system supports intuitive touch-based rotations and zooming functionality, enhancing user interactivity and engagement.
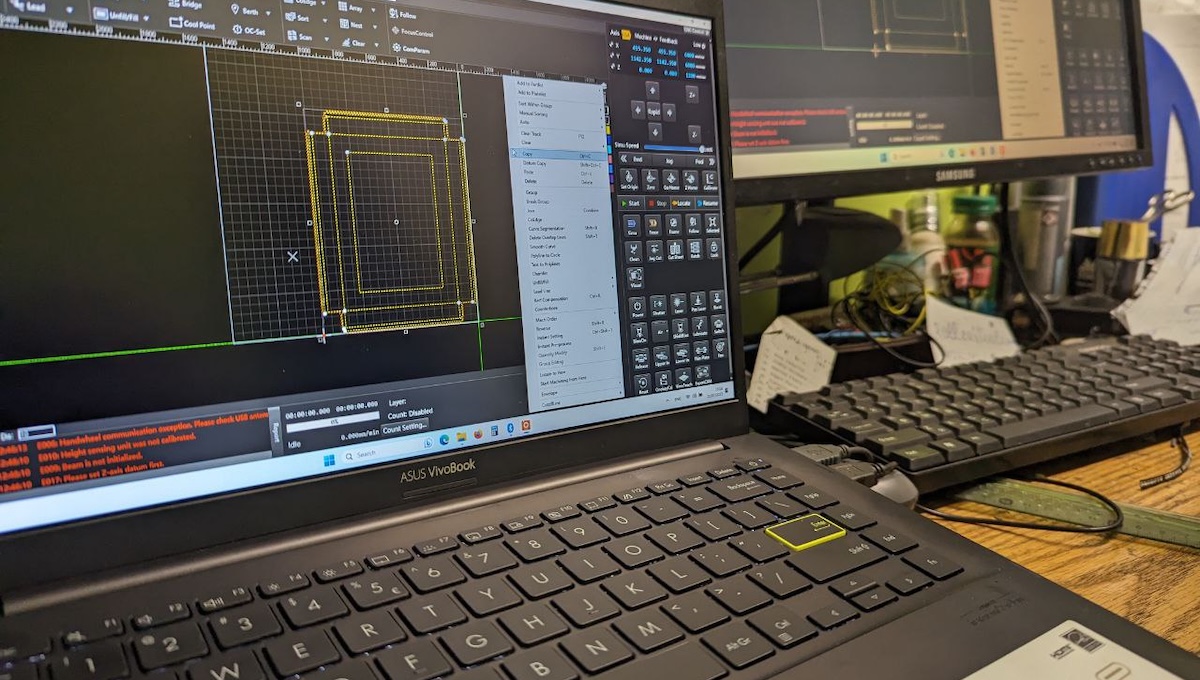
The CNC integration capability
The CNC integration capability allows the factory to capture new orders digitally and automatically transmit approved designs to factory-connected machines, eliminating manual data transfer and reducing the potential for transcription errors. This automation has significantly improved production efficiency and reduced lead times.
Lessons Learned
Technical Challenges:
- Legacy system integration proved imperfect, with product specifications not always reflecting correctly after order synchronisation
- Unique and never-before-ordered product designs still require manual processing, meaning the automation challenge isn't completely solved
- System architecture flexibility is crucial for accommodating future integration requirements and evolving business needs
User Adoption Insights:
- Client preferences vary significantly - while some embrace self-service platforms, others remain reluctant to change and prefer traditional hand-drawn approaches
- Early technology adoption creates competitive advantages before market pressures necessitate change
Market Opportunities:
- Growing demand for remote ordering systems combined with increasing consumer tech-savviness represents significant opportunities
- The company behind Skarda Design saw new customer acquisitions and increased sales as a direct result of the platform's implementation